Amira Alazmi: Electrocatalysts for Redox Flow Batteries – Webinar
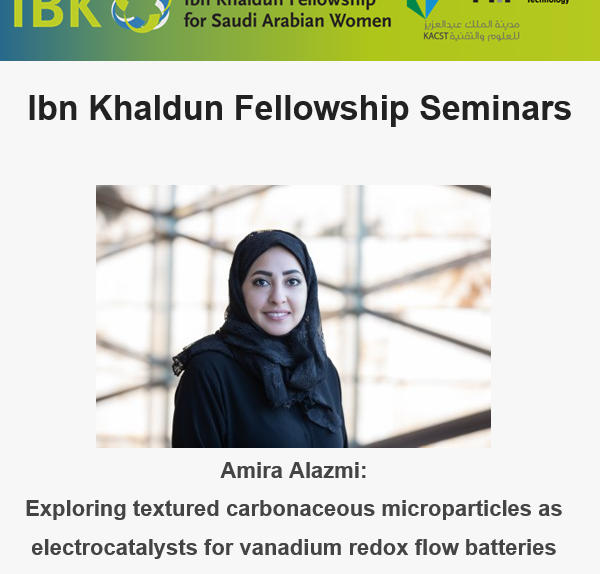
Dr. Amira Alazmi discusses her research with Dr. Fikile Brushett in MIT's Department of Chemical Engineering, specifically her approach to synthesizing carbon-based electrocatalysts and their performance within redox flow cells.
Dr. Alazmi is the Dean of Scientific Research at the University of Hafr Al Batin.
Abstract
Redox flow batteries (RFBs) hold the promise for large-scale energy storage applications due to their independent energy and power scaling, geographical insensitivity, and long cycle life. However, further reductions in system costs are needed for commercial viability. The introduction of electrocatalysts into the porous carbon fiber-based electrodes common to RFBs presents an opportunity for performance enhancement and, consequently, cost reduction. Of interest is the applicability of high surface area graphene which is anticipated to promote ionic adsorption and to improve the electrode performance of a range of redox reactions. In this presentation, we will describe our approach to synthesizing carbon-based electrocatalysts and their performance within redox flow cells. Of interest we will discuss the relative importance of different processing steps (i.e., oxidation, reduction, drying) in the graphene synthesis which control the surface area and pore structure of the resultant powder. The performance and durability of the carbon-based materials deposited into electrodes will be discussed as a function of redox chemistry and cell operating conditions. We anticipate that the strategies described in this presentation are broadly applicable to RFBs and other liquid-phase electrochemical systems.
Webinar Transcript
Transcript for Dr. Amira Alazmi's Webinar: "Exploring textured carbonaceous microparticles as electrocatalysts for vanadium redox flow batteries"
July 29, 2020
Kamal Youcef-Toumi: Good afternoon and good evening, everyone. Thank you for joining us today for this special Ibn Khaldun Fellow seminar.
Today's presentation will be by Dr. Amira Alazmi. A quick background on the program which was launched in 2009-- and this was in collaboration with the King Fahd University of Petroleum and Minerals, or KFUPM, in Saudi Arabia. And it enrolled the first fellow in 2012.
In 2018, we have renewed the contract now with KACST and MIT another 10 years alhumdulillah and with the current KACST sponsorship to continue the work and collaboration with the fellows. And the main purpose is to empower the Saudi women to be leaders in the future. So we even are doing a program.
It is highly competitive, as you know. And it brings between 5 and 10 female Saudi scientists and engineers that are selected for selection or the two selections that happen simultaneously, one in Saudi Arabia by KACST and the second one at MIT by MIT professors and staff members. And so for them to spend one year to conduct research at MIT across the institute. So we are very proud of what the fellows have achieved, the current ones and the previous fellows, and not only in their scientific contributions, but also in their leadership roles that they are making in many disciplines, including industry.
So today, we introduce Dr. Amira's faculty member mentor, Professor Brushett. He is a distinguished professor of chemical engineering here at MIT. A lot of his work involves electrochemical energy conversion, storage, microfluidics, phenomena, interfacial phenomena, catalysts, synthesis, and also tomography.
So I thank him, and also on behalf of the program, for working with Amira and guiding her through the completion of her program at MIT. And I'm going to give the stage to him to introduce her. Professor Brushett?
FIKILE BRUSHETT: Excellent. Well, good afternoon and good evening to everybody. Hopefully you can hear me well. It's my pleasure to introduce Dr. Amira Alazmi.
Amira got her PhD from King Abdullah University of Science and Technology studying under Professor Pedro Da Costa. Her PhD was in chemical sciences. And she did some really quite beautiful work on advancing the synthesis of graphene.
And I think you'll hear some of that in her talk today and how it connected then to the work that she's doing now as an independent faculty member as well as part of her fellowship in our group. After graduating, Amira became an assistant professor in chemical sciences at the University of Hafr Al Batin-- I probably mispronounced that, and I apologize-- as well as serving as the vice dean of scientific research at the university, so quite an important role in managing both university direction as well as direction of one's own independent lab, so, you know, excellent work for her there.
Through the fellowship that was just described, Amira was able to join my group for the past year. And we were very excited to bring her in because of her expertise not just in graphene synthesis-- she'll talk a little bit about how she brought that expertise into our group, and we learned quite a bit from her capabilities and were able to do some very interesting science-- but also her deep expertise in material analysis.
We're a chemical engineering group. We are more users of materials than innovators and understanders of materials. And so Amira really helped us to up our game in that area and better understand how to develop materials that would maybe advance our own technology interests.
It's difficult not to talk about the challenges associated with COVID-19 during Amira's time with us. She had planned a conference presentation. Her work was successful enough that we wanted to give her the opportunity to present in the Netherlands.
And unfortunately, that fell on the wayside. And also she had to leave a little bit earlier to return to Saudi Arabia, but still maintain contact with us through the marvels of Zoom and other internet connectivity. So we were very grateful to have her while we could.
And I will make one note before I turn over the floor to her to tell you about all the wonderful science she did. Her home university was so pleased to have her back, they immediately promoted her to Dean of Scientific Research at that university. So I guess our loss is her gain, but big congratulations to Amira.
And I look forward to hearing her tell you what she's been up to with us. Thank you. The floor is yours, Amira.
AMIRA ALAZMI: Thank you. Thank you, Professor Fik. Thank you all for attending this webinar. I'm very excited to share with you my experience during my fellowship at MIT. And thank you, Professor Fik, for the introduction, again.
I will start to share my screen. And while I'm doing that, please, if you have any questions, submit your questions to the chat. And then I will answer the questions at the end of my presentations.
So actually, as Professor Fik mentioned, my work at MIT was a continuous story of what I have done in my PhD. So I tried to connect what I have learned with the fellowship to get a deep advanced understanding of the material that I am working on. So I was exploring the texture of carbonaceous microparticles as electrocatalysts for vanadium redox batteries, where mainly, I was working in two main projects, the first one exploring the impact of reduced graphene oxide surface texture as an electrocatalyst and redox flow battery. And then the second project was, again, exploring the potential application of activated carbon derived from the palm date seed for redox flow battery.
Speaking about the first project, actually, since here, I am focusing on graphene and graphene oxide, we all know that graphene and reduced graphene oxide can be applied in several applications, for example, for super capacitor, or screen touch devices, CO2 capture, and even for drug delivery. The question is how to make graphene. And actually, to synthesize graphene, there is two main pathways.
The first one actually is the chemical synthesis of graphene on a substrate. Usually it's a transition metal. And one of the famous and most effective methods to produce high-quality graphene is actually the chemical vapor deposition where the graphene is chemically synthesized on the substrate.
And we have a very good quality of graphene. I mean by quality the monolayer graphene that we can obtain where we can maximize the properties of the graphene. However, this method is highly cost. So it's very expensive. And it's not a scalable process.
The other pathway to synthesize graphene is the mechanical cleavage of graphite, the graphite that is existing in our nature, where, actually, the mechanical exfoliation was the first method to produce graphene by exfoliating the graphite, the natural graphite. However, the low throughput and the time consumption to produce graphene using this method is limiting this method to be practical method to be applied and producing larger scale.
Other alternative method of the chemical cleavage is the chemical synthesis of graphene from oxidizing the natural graphite that we have in nature and then reduce it again to have reduced graphene oxide. However, this method produced a low-quality graphene. The graphene produced using this method is low. However, it's a low-cost method to produce the graphene. And actually, this is why we are here focusing on this method, since its cost-effective method, but we want to increase the quality of the produced graphene.
Actually, we look into the literature. And we can see that. And if you are familiar with the field and you have read many publications, you will hear about graphene oxide and reducing graphene oxide too much in the papers.
But however, you can make a graphene chemically using several methods. And you can reduce graphene oxide again using several methods. However, we haven't found any research publication that indicates the differences between the synthesis procedure, how it impacts the final result, that product, whether it's graphene oxide or reduced graphene oxide.
Like, the question here, are all the graphene oxides have the same properties that we are synthesizing using different method? Of course not. But we haven't seen any, like, a comparison study to study the properties of the produced graphene.
And here was our motivation, to select two main synthesis methods of graphene oxide, the most classical method, which is the Hummers' method. And then the second method, it's the improved Hummers' method. And then the main difference between these two method is that in the improved Hummers' method, we are eliminating the sodium nitrate in order to eliminate the toxic gas evolution during the synthesis.
And also in the improved Hummers' method, we are introducing phosphoric acid, which enhanced the oxidation state. We are starting from the natural graphite. And we are oxidizing to have graphene. And then also, we have selected three classical reduction method, which is thermal reduction, the chemical reduction using hydrazine, and also hydrothermal reduction of graphene oxide. We have selected the most common procedures in order to be able to compare the properties of the graphenes.
So this is what we have. We start with graphite. We have HGO, which is from Hummers' method, IGO, which is from improved Hummers' method. And from each graphene oxide, we have the three reduced graphene oxides depending on the reduction method that we have used.
And now, studying the material properties, actually, we can see that the graphite itself, the natural graphite is having the compact and sharp edges morphology, while, after the oxidation, we start to see the separation of the graphite membranes. And the most separation, we can clearly see it in case of IGO compared to the HGO. The unproved method has better separation of the graphite membranes compared to HGO.
Upon the reduction, actually, all the material, all the reduced materials habited similar morphology. So we cannot speak much about the morphology for the reduced graphene oxide here. And looking to the structure and the phase impurity of the material that we synthesized, we have performed XRD, where, actually, we can see the graphite exhibited the characteristic graphite peak at around 28 degrees. And then after the oxidation, this graphite peak has shifted toward lower 2 theta, which means the successful oxidation of the graphite. However, we have observed that the IGO has shifted towards more lower 2 theta, which indicates full oxidation of the graphite compared to the HGO.
Another indication from XRD is that we have the remaining graphite peak here. This indicates to us the HGO method doesn't fully oxidize the graphite material. After the reduction, we can see that the graphene oxide peak has shifted back towards the graphite position, which means the material has been reduced.
However, in general, we can see that the full width half maximum in case of all IGO material is larger than the full width half maximum that's related to the material produced from HGO material. And this gives us indication that this material has a small grain size. Also it has more defect compared to the material produced from HGO.
And to study the defect in any carbon material, we need to learn that from Raman. So we performed Raman, where actually, we can immediately see that, from the ID over IG, ID the D peak is the defect peak and the G peak is the graphite peak, where, from the ratio, we can conclude how much this material is defected. So looking to the HGO and IGO, we have seen that there is a higher ratio in case of HGO, which indicates our observation in XRD.
This material has more density of defect compared to HGO. And this is applied also to the reduced material. It was more defected than the material produced from HGO.
Looking to the XPS, actually, it has been also confirmed that the IGO material is more oxidized compared to that HGO. And after the reduction, from XPS, we have confirmed that all the material reduced to produce the graphene oxide. However, the reduction degree was a slight difference between reduction method and another method.
What we have done actually here, we have collected all the reduced graphene oxide material that we have obtained. And we have applied it for super capacitor application. What we have found here, in general, the material that's produced from IGO has higher capacitance than the material produced from HGO.
And more specifically, looking to the IGO material, we found that the hydrazine, or the chemical reduction, and the hydrothermal reduction of IGO exhibited higher capacitance compared to the other reduction method. So in order to improve this material more and to study more this material, we need to select one of them to further enhance the properties of the material. So the selection between the hydrothermal and the hydrazine actually was not too difficult, since, by using hydrazine, we are using toxic material to reduce graphene oxide, while, in the hydrothermal reduction, we had using only water. And we are reducing at 180 degrees C. So we have decided to go with the hydrothermal reduction method in order to further enhance the material and to maximize the capacitance of the material.
So what we can learn from here, by optimizing the oxidation state of graphite and then the reduction state of graphite, we have 10 times more capacitance, which hasn't been discussed before in the literature. So this brings to us the question if we can do better than that. But at the same time, as carbon , people we want to keep it only carbon without any additional functionalization to eliminate the cost of the material and also without adding any particle or adding any additional synthesis step to it, so just keep it as simple as we can.
So this draws our attention. So we have focused on the oxidation and the reduction step. What is remaining for us is the post-synthesis step. When we obtain our material, we will immediately dry the material.
So this point hasn't been discussed in the literature as well. So we looked into the literature. And we see that, when you obtain your synthesized material, either you dry it using vacuum or open-air drying. Or even you can use freeze drying to use your powder material.
Well here, our motivation was from the biological specimens, actually, where, in order to image or to make electron microscopy imaging for any biological specimen, you need to remove all the water in order to subject the sample to the SEM. However, you need to repair the 3D structure of the biological specimen to see all these details that we are seeing here. So how do they do that? They dry the material at the critical point, where, at the critical point, the surface tension is zero.
So the water can be removed from the sample without destroying or collapsing the structure. And this is what we need in graphene. We want to remove the water. At the same time, we reserve the separation of the graphite that we did during the oxidation and the reduction. And this is actually the main issue with the graphene synthesis, because we have collapse of the graphene whenever we dry the material, which means we are losing the surface area. And we are losing the porosity, which will reduce the properties of the material.
The question now, again, is how to do this in chemistry, because the biological specimen, it stand by itself. You can subject it to the chamber under very high vacuum. And you collect your sample without losing the sample. Now we are working here in powder material under very high vacuum. So there is a huge chance that we lose the powder under the vacuum. And the other concern, not only saving the powder material, we want to subject it to the chemical-- to the critical point of drying. At the same time, we don't change the structure or we don't have any chemical changes. So we have the same material, but only dry it.
So for this, I have designed the sample holder that can be subjected to the CPD machine. And this sample holder is made of Teflon and are very small balls mesh, where it can allow the CPD process. At the same time, it saves the powder material.
So this is the CPD machine, or the Critical Point Drying machine, where we subject our synthesized reduced graphene oxide or graphene oxide. And then we start the process of the critical point drying. And then, finally, we collect, for the first time, the reduced graphene oxide which is dried using critical point drying.
And this is actually our strategy where we oxidize the graphite. And then we reduce it. And then we introduce the new method. But also we need to compare it with the existing method in order to validate our method. So we actually have dried the material using freeze drying and vacuum drying to see whether our new method is effective or not.
So this is what we have. We have synthesized one batch of graphene. And then we divide it into-- graphene oxide, we divide it into three parts. And then we vacuum dry it, freeze dry it, or the CPD drying. And then we reduce it using hydrothermal, the method that we are focusing on. And then after that, we dry it with the respective drying method.
And actually, from the visual looking of the sample with the same weight of the sample, we can see that the CPD drying method occupied more volume compared to the vacuum-dried method with the same mass, which means this material has a higher surface area compared to that vacuum material. And this, we can actually see it under the electron microscopy, where we can see the vacuum out of the freeze dryer has a compact structure, where here we have more separation of the graphite basal plane. So by using this method, we have revealed the 3D structure of the reduced graphene oxide. So we don't have any collapse.
And from performing XRD and XPS, we have confirmed that we don't have any structural or chemical changes. So all the materials are reduced graphene oxide. The difference only is the separation of the graphite layers. Well actually, the main difference between the material, we can see it here performing the N2 structure analysis, where, actually, the CPD material exhibited a mesoporous structure with a pore size about 20 nanometer compared to the microporous structure, about 1 nanometer, of the reduced graphene oxide that's dried using vacuum or freeze drying, which means this material has-- the [INAUDIBLE] has been collapsed and shrinked using this classical drying method.
And one other finding that we have is the CPD material has a 360 square meter per gram compared to about only 40 square meter per gram in case of the normal drying method. And this actually was the highest surface area reported for the hydrothermal reduced graphene oxide. And we can relate to that due to the several stresses that the material, when we subject it to vacuum or freeze dryer, we are subjecting our material to the surface tension. So the material lead to collapse during the water removal. However, as the zero surface tension using the critical point dryer, we can remove the water without any collapse or any subject-- without subjecting our material to any collapse or stresses.
So we applied the new material, the new dried material and super capacitor as well. And we can see that the CPD material actually exhibited 2-times capacitance compared to the vacuum and freeze-drying method. And also, this material has exhibited very good stability.
So what we have learned, again, from here, is that, by optimizing the synthesis steps, which is the oxidation and the reduction, and on top of that, by paying attention to the drying step, which is the first synthesis step, we have 18-times-better capacitance, which will draw the carbon community attention to pay attention how to select the oxidation, and the reduction, and the post-synthesis procedure, depending on the application. And also, this capacitance obtained here, it was the highest reported capacitance for hydrothermal reduced graphene oxide in the literature.
So actually, this was my motivation to work in MIT, where I started with this sample, since, after understanding the impact of synthesis method in graphene oxide and then also I applied the two graphene oxide methods that I obtained for CO2 capture-- I'm not going to explain this. I'm just showing that we have applied it for CO2 capture. And we found that the IGO material has better CO2 uptake compared to the HGO.
And also I have applied it for magnetic resonance and by adding nanoparticles. And I have found that the material brought from IGO has better performance than the material applied from HGO. And also, we apply this for super capacitors, and paying attention to the both synthesis. And again, in general, the IGO material exhibited better performance in different application, as you see. So this was my aim, to draw all the carbon community attention from using the classical Hummers' method to use the improved Hummers' method.
Here, in MIT, actually, I worked on vanadium redox flow battery, which is another application, to further confirm the hypothesis that the IGO material and the both synthesis step is very important to focus on. So in vanadium redox flow battery, actually, it's one of the interesting application, because this kind of battery has a large capacitance, long life cycle, and also a fast response time. And the vanadium redox battery actually is limited by the positive side reaction, where, beside the electron transfer, we have hydrogen and water, which makes the positive side is-- all the vanadium redox battery limited by the positive-side reaction. And this is why, actually, we need to develop an electrode that assists the kinetic of the vanadium redox battery in order to have better performance. And actually, carbon felt's used as electrode in vanadium redox battery usually, because it has outstanding mechanical strength and high intrinsic stability in the [INAUDIBLE] medium.
However, it has some drawbacks, for example, low device efficiency, which leads to have the scientists to decorate the carbon felts using a noble metal. And the noble metal, actually highly cost method to assist the kinetic of the vanadium redox battery. As an alternative, we can decorate the carbon felt using graphene or reduced graphene oxide, which will provide excellent conductivity, large specific area. And also, it's inert in a very acidic condition. So we see that the graphene is a very good candidate to apply in the vanadium redox battery.
So the strategy here is to know that whether the surface area will have an impact in the vanadium redox battery, as we have a very high surface area and the CPD material compared to low surface area in case of vacuum drying. Also, another point that we need to study is the porosity. Since we know that the CPD exhibited the mesoporous material, while the vacuum one exhibited the microporous material, so we have a variety in the surface area and the porosity. So we can study the two conditions at the same time. Also, we have studied, if we thermally treated the carbon felt substrate before the addition of the reduced graphene oxide on the carbon felt, whether it will enhance the electrochemical performance or not.
So we have deposited our graphene on the carbon felt either using CPD graphene or vacuum graphene. And we have confirmed the deposition of the material from SEM and from Raman as well. And we have to studied the electrochemical surface area of both the CPD graphene and then the vacuum graphene.
As we can see, the carbon felt alone has very low surface area. And we can read that from the current, where the vacuum exhibited higher current than the carbon felt, with the maximum current obtained using the CPD material. What is surprising here, when we look into the surface area of CPD material and vacuum material, we can see the electrochemical surface area here is similar. It's not so different.
Again, when we thermally treat the carbon felt and then deposit the graphene on the carbon felt, we have seen that the surface area, the electrochemical surface area is compared. This gives us indication that we are eliminating the fact of-- the different surface area, since the electrochemical surface area is the same. And what we are studying here is the impact of the porosity of the material, whether the micropores or the mesopores will affect our electrochemical performance.
Applying the vacuum material and then the CPD material, we can see that the CPD, in red, exhibited better electrochemical performance than the vacuum one. Also, in terms of resistance, the resistance was lower in case of CPD compared to the vacuum one.
Here what we have done to further optimize our study, we make fist deposition on the carbon felt with a certain concentration. And then to eliminate the fact that, if we add more material, we would have more electrochemical performance, so we have addition of the second deposition on the carbon felt. And what we have learned from here, that the second addition has a very slight improvement than the first deposition, which means that we can stick to the first deposition without usage of more material. So we can lower the concentration or lower the amount of the material that we are using.
So we went to thermally treat the carbon felt substrate before that the deposition of graphene. And we study the CPD electrochemical performance, where we can see that, when we thermally the carbon felt, the CPD has exhibited more electrochemical response compared to the pristine carbon felt. And also, we can see the resistance has minimized.
Also we studied the rate and the stability of the material, applying different current. And we can see this material exhibited a very good Coulombic efficiency. And in terms of stability, the material was very good, shows very good stability up to 100 cycles with very good Coulombic efficiency, as we can see here.
So what we can learn from this project is that, when we apply the vacuum graphene, and then applying the CPD graphene, we have enhanced the electrochemical response. And on top of that, after thermally treated the substrate, we have further maximized the electrochemical performance of the material. And this actually drive our attention of we can further maximize our electrochemical performance, and this time, going green and using biomass also, as a carbon person, keep it only carbon without any functionalization or any addition of particles.
And this takes us to the second project, which is making graphene from the palm date seeds. As we know, Saudi Arabia is one of the world's leading countries growing fresh dates. So if I am thinking of biomass, I would go for dates immediately to synthesize-- to obtain carbon from dates.
So we start from there. And then we hydrothermally the carbonize it. We obtain carbon. And then after, that we activate the carbon using either CO2, or KOH, or phosphoric acid activation in order to have the first material that can be applied for electrochemical application.
So the goal here is to have a very high-surface-area material but brought greenly from the dates or biomass. And then again, we study the effect of the porosity and in vanadium redox flow battery. So this is briefly the synthesis procedure.
We start with dates. We hydrothermally carbonize it. And then we have the carbon material. And then after that, we activate. And then we have the activated carbon.
The very porous and high-surface-area activated carbon, we can see, the surface area it reaches up to 2,300 square meter per gram, which is a very good surface area brought in from biomass. And I started with these two samples. The aim was, comparing all of the materials, but, due to COVID, I just studies these two materials.
And then when we characterized the material, we can see that, depending on the activation process, for example, the CO2, KOH, and phosphoric acid, the material morphology changed. And then the maximum porosity, we can see it, and the maximum rough surface, which indicates higher surface area, we can see it from KOH. And looking to the [INAUDIBLE] analysis, we can see that this material exhibited different surface texture information.
For example, some of this material is microporous material. Some of them is mesoporous material. However, this material has a mesoporous nature, but not all of the material has similar porosity nature. For example, the PDS8 has the maximum mesoporous population compared to other material.
So what we are studying here, the PDS8 and PDS9, where they have really different porosity information. We applied this for vanadium redox flow battery. And we found that, compared to the pristine carbon felt, the substrate that we had using, we have a very good electrochemical response. And also here we can see that the resistance has been decreased.
Looking to the second material, which is phosphoric acid activation, we can see that this material as well has a better performance compared to the carbon felt, but not compared to the PDS8. And then we thermally treated, following the procedure, we thermally treated the carbon felt before we deposit our material. And we can see that there is an enhancement, further enhancement. If we can compare, for example, here, PDS9, it's about 180, and here it's approaching 250 pore density, which means that we have enhanced the electrochemical response of this activated carbon material.
And as a conclusion from these two projects, actually, from the first one, we have learned that, by applying-- by paying attention to the synthesis conditions and to the post-synthesis procedure, we successfully have a very good electrochemical response in redox flow battery. And then by using a biomass that's brought from the palm date seeds, we have a very good electrochemical response for vanadium redox flow battery. Actually post IBK, as Professor Fik mentioned that, I just get promoted as a Dean of Scientific Research in the whole university. So I'm moving to Hafr Al Batin from Nairyah.
Also here, I would like to especially thank Professor Fik to give me this opportunity to join his group and learn from every member in his group. And under his supervision and guideline, I have learned a very good knowledge during this fellowship. And also I would like to thank Cara, and Charles, and Professor Brushett's group.
Also I would like to thank Professor Boudreau for sending me the sample that I have synthesized while I was in KAUST, thank University Hafr Al Batin. And I wouldn't be at MIT without IBK. So I would like to thank you, Professor Kamal, Theresa, Dorothy and Nadiyah, and everyone in IBK.
Thank you so much for giving me this opportunity. And thank you all for being here and listening to my speech. I will go to the chat. Thank you so much. I will go to the chat. I will see if there is any question.
Nadiyah Shaheed: Alhumdullilah, thank you so much, Amira. And I just sent another reminder, even though you prefaced your webinar, that all attendees can submit questions through the Zoom chat feature. Just type them in. And Amira will answer them.
Kamal Youcef-Toumi: Thank you, Amira. And maybe I'll take a minute to introduce to the participants the team that makes IBK work. There is Theresa Werth, and also Dorothy Hanna, and Nadiyah Shaheed, yes. Yeah, this is a great presentation. Thank you, Amira. And congratulations on your new position.
I'm looking also at the chats. Maybe I can ask a question while we are waiting for the chat. This is not my area, by the way. It seemed that one of the key things that you emphasized in obtaining, like, super capacitor performance was the large area that one gets-- is that correct-- from the process? So yeah, if this is the case, so what is happening is that, like, for the area to be larger, is there-- like, are there pores that are being formed in the material? Or what is going on physically that is increasing this area?
AMIRA ALAZMI: Thank you, Professor Kamal for the question. OK, so this is all about enhancing the electrochemical requirements. If we think of graphite, before oxidizing and reducing it, if you look to the very close and book, and it's a very huge book, the graphite, you can think of the graphite, it's each page of this book. If you are opening the book or opening the spaces between the books, you you are allowing the ions to enter between the pages, which means you are allowing the ions to access between the graphite layers, which means you are accessing more surface area, you are accessing more conductivity [INAUDIBLE].
Kamal Youcef-Toumi: Thank you. Very good. I think there is a question. What kind of defects are you expecting to have in your materials?
AMIRA ALAZMI: Yeah, I will go to Raman. And I will explain the defects. Actually, the defects here can be defined into two stages. The first stage, when we synthesize the graphene oxide from graphite-- OK, so this is Raman.
Actually, the first stage when we-- we have graphite. So as you can see here, there is no defect peak in graphite. After that, we are introducing a functional group by making the graphene oxide we are introducing ethoxy OH group. So we are making defect by introducing functional group.
So we are adding more sp2-- sp3, sorry, sp3. As we know, graphite are sp2. So we are adding sp3 carbon. So this is the defect. After the reduction, we are removing all the functional group. We can define the defects here by the vacancies that occur in the graphene oxide after the removal, the harsh removal of the oxygen functional group from graphene oxide. I wish I answered the question.
Kamal Youcef-Toumi: Another questions?
Theresa Werth: Maybe I'll read it just for the purposes of our recording so our future guests can hear it. So for the material that was prepared with the dates, which are around the micro size, is there a work in progress to decrease that to nano size to increase the surface area and other properties?
AMIRA ALAZMI: OK, here I will just define the micro size. OK, the micro size, I mean, 1 nanometer to 2 nanmoeter, and then the meso size from 2 nanometer to 25 nanometer. And then the macro size are 25 to 50 nanometer.
So we are speaking about nano-sized balls. Actually, it's a very, very small porosity, which is from 0 to 2 nanometer, actually. So this is the lowest pores that you can get from this material.
Kamal Youcef-Toumi: Maybe I'll ask a question. Maybe this was in slide 29 or 30-- I don't remember-- where you had the curves, our current versus the potential.
AMIRA ALAZMI: 29.
Kamal Youcef-Toumi: You can just press 29, type 29 and Return. You are in presenter. Yeah, these, this slide here. So yeah, so here, you're plotting current versus the potential.
And then in all of these plots, there is some behavior that looks to me as a hysteresis effect or a hysteresis phenomenon. So if that is the case, so that means, in this process, there are losses. There is dissipation and loss of energy.
And then the wider these loops are, the thicker or the fatter they are, the more losses there are or there is, and the more loss is in the process. And then the thinner they are, the slim, that means less losses. Is this, my understanding, correct, in reading these graphs? Or is there something else going on?
AMIRA ALAZMI: OK, actually, you mean the hysteresis here between this lines?
Kamal Youcef-Toumi: So these graphs, you know, to me, they look like a hysteresis loop. So for example, you have the potential at zero. So then you increase it, let's say, all the way to 0.2. So it goes along one curve.
And then you start decreasing. It goes not the way it came. It comes back from another direction. And then you go negative from 0 to minus 0.2. And then it continues that way.
And then now you start increasing. And so if it was a straight line or it was just one curve, so that means there is no losses or no hysteretic phenomenon. But when they look like this, when we plot the current and these, we call them conjugate variables, the current and the potential, then you have these losses. Is that what is happening here or something else?
AMIRA ALAZMI: OK, well I think what is happening here is something else in terms of how we can read this one. This is the current. As long as, if you call it hysteresis, as we have a larger hysteresis, we have a large current, which means we have more conductivity.
We have more accessibility of the electrolyte to reach the electrode, which means we have a better electrochemical response. However, the behavior here, for example, if we look to the black line here, what we are changing here is this current rate, by means that we are scanning from slow scan rate to 200, which is very high scan rate. When you are scanning slowly, so you have time for the reaction to occur.
So you have the great capacitance behavior, which is the black one. Whenever you are increasing the scan rate, as a kinetic factor, you don't have really time for the reaction to occur. So this is why it's moving, giving you this eye shape.
Kamal Youcef-Toumi: And the-- and what you're applying is also, is the potential?
AMIRA ALAZMI: Yeah, the potential.
Kamal Youcef-Toumi: And it goes from minus 0.2 to plus 0.2 volts?
AMIRA ALAZMI: Yeah, we go like this. We go like this as a circle. So each one, each line, it's a different experiment.
Kamal Youcef-Toumi: And you are measuring the current like in this case?
AMIRA ALAZMI: We are applying potential. And we are measuring the current.
Kamal Youcef-Toumi: Yeah, OK. Yeah, you may want to look into this, because this is, in electrical systems or a system that has this kind of behavior, it means that there are some losses in that process, dissipation.
AMIRA ALAZMI: Yeah, if we consider it as the losses, it's due to the fast kinetic of the reaction that we don't have really time for the reaction to occur.
Kamal Youcef-Toumi: Yeah, thank you.
Dorothy Hanna: I have a question, Amira.
AMIRA ALAZMI: Please.
Dorothy Hanna: You mentioned that this might be the processing, that these seeds might be a way of getting green energy storage. And I was wondering the side effects or the other materials that are produced by processing the date seeds to get the graphene from them. Like, what does that create?
Theresa Werth: Like what byproducts?
Dorothy Hanna: Yes.
AMIRA ALAZMI: Yeah, actually, we can't really call, like, whenever we are doing synthesis, we can't have 100% green process. However, when we are making graphene oxide from the natural graphite, we are using acids. We are using oxidizing agents, which is very harsh to the environment.
While we are starting from having carbon from the dates, we are starting from the worst of the material, from the biomass. And then we are carbonizing. What would be the harsh byproduct here when we activate the carbon using KOH or phosphoric acid, this would be a harsh to the environment somehow, yes.
Dorothy Hanna: Thank you.
Kamal Youcef-Toumi: Very good, yeah.
Theresa Werth: I had a question too. And perhaps I missed this in the top, because I do not have the technical background to hang with all of this. But I was really impressed with this new graphene development process that you have created. And I think what you were saying is that you sort of were testing it with some sort of existing processes, but I was wondering if, given the better properties of this new graphene, does that suggest applications that maybe were not possible with the previous methods? Or how do you think this will enable people to use the graphene in different ways?
AMIRA ALAZMI: Actually, it is not to apply graphene to applications that graphene has never been applied for it. Graphene applied for most of the application-- however, it just enhanced the properties in way that, for example, if I want a micropore the graphene, I would dry the graphene using vacuum drying. If I would like to have a mesoporous graphene, I would go with the CPD drying process. And this, actually, I can tell you two application where you can select.
For example, if you are working in lithium ion battery, you would definitely go with drying graphene using vacuum, because you micropores which is very small pores, because in lithium, with lithium, ions very small, so you don't need the mesoporous structure. While you are walking in super capacitor, you are working with large ions, for example, SO4. You need the mesoporous structure. So this is to allow the scientists to design the material depending on the application, if they are working in super capacitor, in lithium ion battery, in vanadium redox battery, so for the scientists to select the synthesis procedure depending the application needs.
Theresa Werth: Got it. Thank you. Yeah, that's really helpful and exciting. Thank you very much. And thank you for this wonderful talk. Thank you so much.
Kamal Youcef-Toumi: Very good, yeah. Any other questions? OK yeah, so if there are no more questions, then thank you, Dr. Amira for the great presentation, for your new position, and your responsibilities. And we also thank Dr. Brushett for supervising your work and being with you before all this time. And we hope that you and Professor Brushett and this team, that you can continue your relationship, and the research, and collaboration in the future.
AMIRA ALAZMI: Thank you.
Kamal Youcef-Toumi: Thank you, everyone. And we will make an announcement for another seminar sometime later, is that right, Nadiyah?
Theresa Werth: Stay tuned for more.
Nadiyah Shaheed: It is. We have a seminar series coming up which we'll be announcing and publicizing, as well as individual IBK fellow seminars that they will be presenting. But we have a seminar series coming up that we'd love everyone to participate in. So look out for announcements, please.